EPRO MMS 6350 Digital Overspeed Protection System
Description
Manufacture | EPRO |
Model | MMS 6350 |
Ordering information | MMS 6350 |
Catalog | MMS 6000 |
Description | EPRO MMS 6350 Digital Overspeed Protection System |
Origin | Germany (DE) |
HS Code | 85389091 |
Dimension | 16cm*16cm*12cm |
Weight | 0.8kg |
Details
Digital Overspeed Protection System with PROFIBUS -DP interface
DOPS, DOPS AS, DOPS TS
● Systems DOPS and DOPS AS SIL3-
certified
● PROFIBUS-DP Interface: (optional)
● Microcontroller based 3-channel measuring system
● High safety level due to password protection at each of the monitors
● Up to 6 limit values per channel
● Two current outputs per channel with zoom and dual current function, one
of them electrically isolated
● Mutual comparison of pulses and output signals between all channels
● Redundant power supplies for monitors and backplane
● Self-test functions for electronic circuits and sensors
● Simplified fault detection by display messages in plaintext
● Electrical isolation of binary input and output signals
● Wiring by means of preformed cables and converters in the control cubicle
● RS 232 interface for input of parameters
● RS 485 interface for data exchange with the host computer
● Hot swap of boards during operation
Application:
The speed measurement and
overspeed protection systems
DOPS and DOPS AS serve the
measurement of speeds and the
protection of inadmissible
overspeeds at rotating machines.
The DOPS systems in combi
nation with safety shut-off valves
are suitable to replace older
mechanical overspeed protection
systems.
With the consistent three channel
design, starting with the signal
detection via signal processing up
to the evaluation of the measured
speed, the system offers the
maximum safety for the machines
to be monitored.
Safety relevant limit values (e.g.
overspeed limits) are submitted to
the post-connected fail-safe
technique.
Thus it can be ensured that beside
operational safety, the protection
function on a high level standard is
met as well.
The integrated peak value memory
permits reading out the maximum
speed value that has occurred
before the machine was switched
off. This function provides important
information for evaluating the
mechanical machine load caused
by the overspeed.
Alarm outputs and error
messages are output as potential
free relay outputs and as short
circuit proof +24 V voltage outputs.
The alarm outputs, combined in 2
out of 3 logic, are also available as
potential free relay contacts.
The system includes an extended
fault detection function. The three
speed sensors are continuously
checked on operating within the
permitted limits.
Moreover, the channels mutually
check and supervise the output
signals of each other. If the internal
fault detection circuit detects an error,
this will be indicated via the output
contacts and shown on the display as
plaintext.
By means of the the PROFIBUS DP
interface the recorded data can be
passed on to host computers.
By using prefabricated connection
cables and screw terminals, the
systems may be integrated
economically in 19“ cabinets.
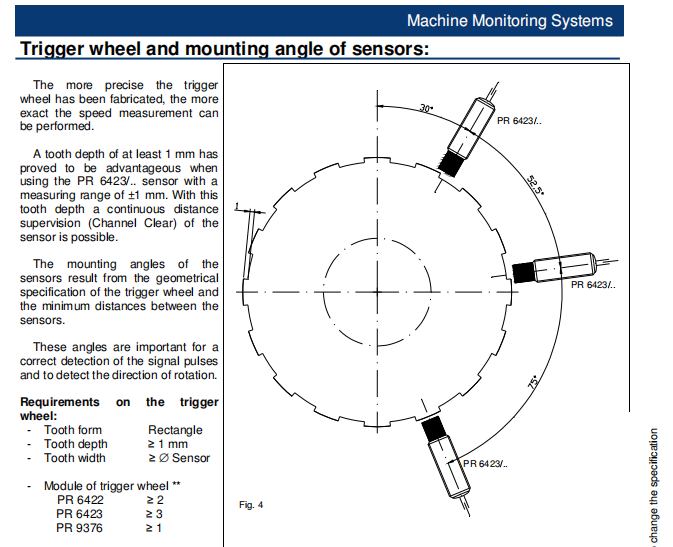